Understanding Elbow Hose Connectors: Your Comprehensive Guide
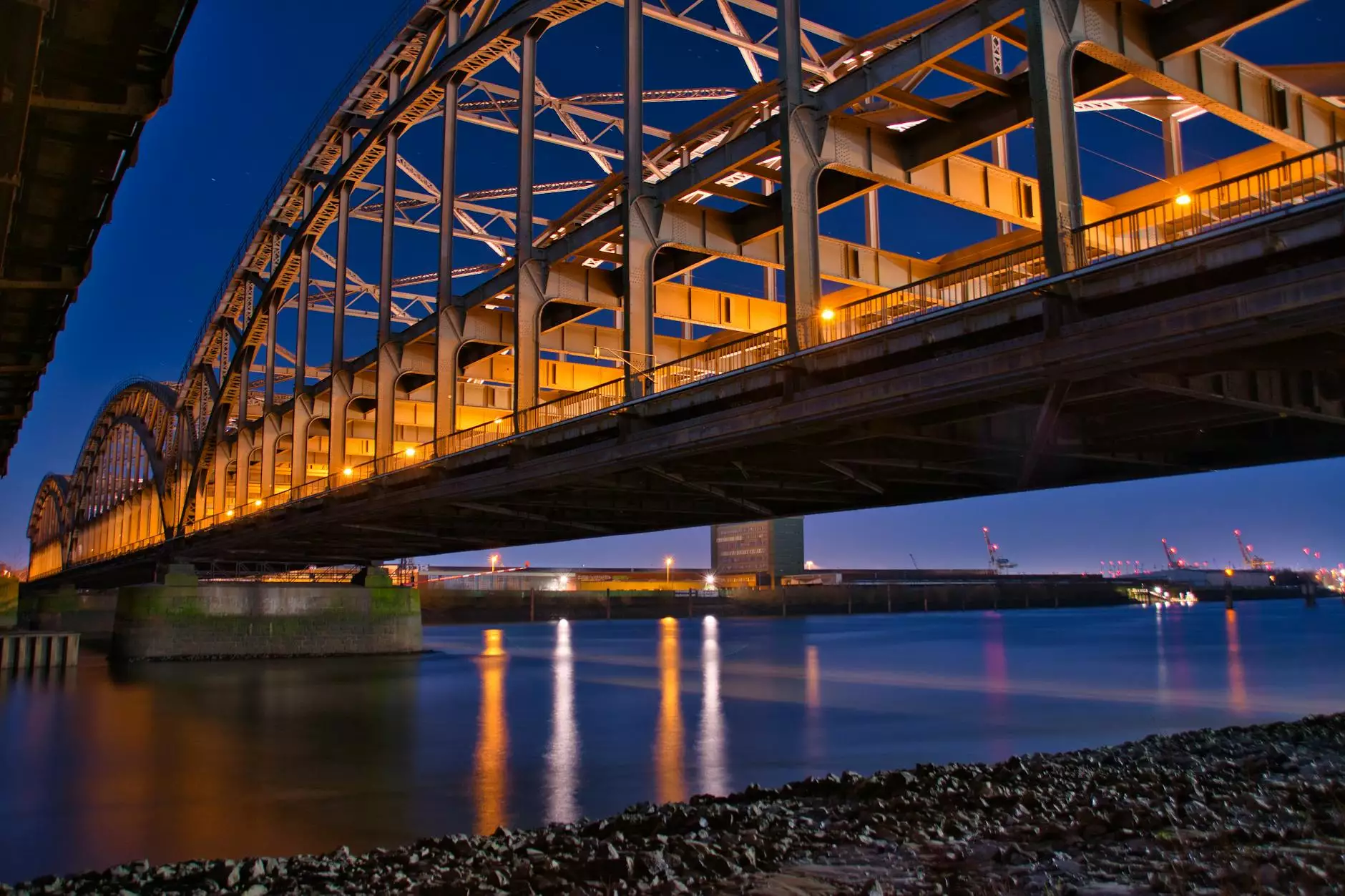
Elbow hose connectors are vital components in various fluid transfer systems, serving as essential joints that facilitate changes in direction within a hose assembly. In this article, we will delve into the intricacies of elbow hose connectors, exploring their types, applications, advantages, and best practices for selection and installation. Whether you are in the manufacturing, agricultural, or automotive industry, understanding how to effectively utilize these connectors can greatly enhance your operations.
What is an Elbow Hose Connector?
An elbow hose connector is a fitting designed to connect hoses or tubes at an angle, usually at 90 degrees or 45 degrees. These connectors allow for a more streamlined flow of liquids or gases, minimizing turbulence and ensuring efficient fluid transfer. They come in various sizes and materials, catering to a wide range of industrial standards and requirements.
Types of Elbow Hose Connectors
Understanding the different types of elbow hose connectors available in the market is crucial for making informed decisions when it comes to hose assembly configurations. Here are some common types:
- Standard Elbow Connectors: Typically available in 90-degree or 45-degree angles, these connectors are suitable for various applications where a standard directional change is required.
- Reducing Elbow Connectors: These connectors facilitate a change in the diameter of the connecting hoses, allowing for a seamless transition between hoses of different sizes.
- Barbed Elbow Connectors: Featuring small barbs, these connectors provide a secure grip on the hose, ensuring minimal leakage. They are often used in applications requiring high-pressure fluid transfer.
- Threaded Elbow Connectors: These connectors have screws and threads for secure, leak-free connections, making them ideal for high-pressure systems.
- Swivel Elbow Connectors: Designed to rotate, these connectors allow for greater flexibility in hose routing, enabling adjustments without straining the hoses.
Applications of Elbow Hose Connectors
Elbow hose connectors find applications across various industries due to their versatility and efficiency. Some of the most common applications include:
- Pneumatic Systems: Used to connect hoses in air-based systems, these connectors help in guiding the airflow efficiently.
- Hydraulic Systems: In hydraulic machinery, elbow connectors assist in directing fluid from pumps to cylinders.
- Automotive Applications: Commonly used in vehicles for coolant lines, fuel lines, and power steering hoses, providing critical connectivity.
- Industrial Equipment: In manufacturing, these connectors manage fluid transfer in various machinery, from conveyor systems to robotic arms.
- Agricultural Machinery: Used extensively in irrigation systems and farming equipment, ensuring effective water and chemical application.
Advantages of Using Elbow Hose Connectors
Utilizing elbow hose connectors in your systems comes with several benefits, making them invaluable components for both industrial and commercial applications:
- Space-Saving Design: The angled configuration allows for efficient use of space, particularly in tight setups where straight lines aren’t feasible.
- Enhanced Flow Control: By minimizing bends and kinks, elbow connectors help maintain optimal flow rates and pressure levels.
- Durability: Made from robust materials like brass, steel, or high-grade plastics, these connectors offer resistance to oxidation, corrosion, and wear.
- Easy Installation: Most elbow connectors are designed for straightforward installation, often requiring minimal tools and expertise.
- Versatile Compatibility: Available in various sizes and configurations, elbow hose connectors can be adapted to suit different hoses and tubing systems.
Choosing the Right Elbow Hose Connector
When selecting an elbow hose connector, it is essential to consider several critical factors to ensure compatibility and efficiency. Here’s a comprehensive guide on what to keep in mind:
1. Material
The choice of material for your elbow connector depends on the application and the media being transported. Common materials include:
- Brass: Excellent for high-pressure applications; it resists corrosion and is safe for potable water.
- Stainless Steel: Ideal for harsh environments and chemical substances, offering superior durability and resistance to corrosion.
- Polypropylene: Lightweight and resistant to chemicals, making it suitable for various industrial applications.
2. Size and Flow Rate
Choosing the correct size is crucial to ensure a proper fit and optimal flow rate. Measure the inner diameter of the hose to match it accurately with the connector.
3. Angle
The angle of the connector significantly affects the overall flow dynamics. Consider whether you need a 45-degree or 90-degree elbow based on your specific routing needs.
4. Pressure Rating
It’s vital to confirm that the elbow connector's pressure rating exceeds that of your system. This consideration can prevent failures that could result in leaks or ruptures.
Installation Best Practices for Elbow Hose Connectors
To ensure the longevity and reliability of your elbow hose connectors, follow these installation best practices:
- Clean the Connection Points: Ensure that all surfaces are free from dirt, debris, and moisture before installation.
- Use Proper Tools: Utilize the correct tools for tightening and securing your elbow connectors without over-torquing.
- Check Alignment: Ensure the hoses are aligned correctly to prevent undue stress on the connectors.
- Inspect After Installation: Regularly check for leaks and corrosion, especially in high-pressure systems.
Common Mistakes to Avoid
When working with elbow hose connectors, awareness of potential pitfalls can avert issues:
- Neglecting Specifications: Always follow manufacturer specifications regarding size, material, and pressure ratings.
- Improper Tightening: Over-tightening can lead to damage, while under-tightening may cause leaks.
- Ignoring Environmental Factors: Consider the operating environment and choose materials that can withstand specific conditions (e.g., extreme temperatures or chemicals).
Conclusion
In conclusion, elbow hose connectors are indispensable components in many systems that require fluid transfer. Understanding their types, applications, advantages, and installation best practices can significantly affect the performance and reliability of your operations. As you venture into selecting the right connectors for your needs, consider the insights shared in this guide to make informed decisions. Always prioritize quality and compatibility to ensure optimal functionality within your industrial or commercial setups.
For more high-quality fittings for sale, visit fitsch.cn and explore our diverse range of products designed to meet your specific needs.