Plastic Injection Molding Manufacturing: A Comprehensive Guide
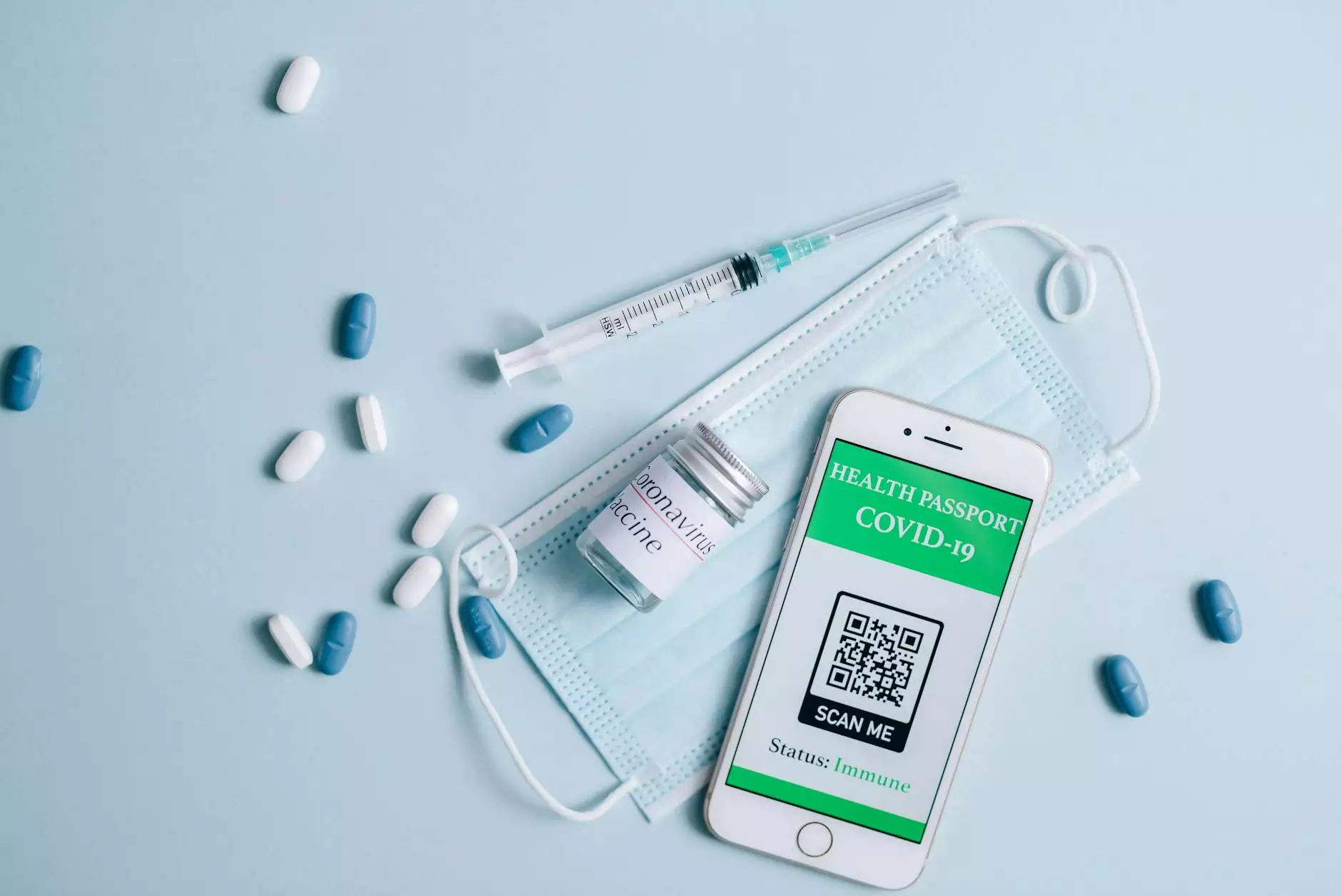
In the rapidly evolving landscape of manufacturing, plastic injection molding stands out as a game-changing technology that enables the creation of a myriad of products with precision and efficiency. At DeepMould.net, understanding this process is crucial for businesses looking to enhance their manufacturing capabilities, particularly in the realm of metal fabricators. This article delves into the essential aspects of plastic injection molding manufacturing, exploring its processes, advantages, applications, and future trends.
What is Plastic Injection Molding?
Plastic injection molding is a manufacturing process that involves injecting molten plastic into a mold to create a specific shape. This technology is widely used due to its ability to produce intricate designs at high volumes with minimal waste. The process begins with heating plastic granules until they become malleable and can be injected into a mold. Once cooled, the mold is opened, and the solidified part is ejected, often requiring minimal finishing.
How Plastic Injection Molding Works
The plastic injection molding manufacturing process involves several critical steps:
- Material Selection: Choosing the right type of plastic is fundamental. Common materials include ABS, polycarbonate, nylon, and polypropylene, each offering unique properties suitable for different applications.
- Designing the Mold: Designing an effective mold is crucial. This process should account for shrinkage, draft angles, and part complexity, impacting the overall quality of the final product.
- Melting the Plastic: The selected plastic is fed into a hopper and heated until it turns into a liquid state. This transformation is typically done in a heated barrel with a rotating screw system that helps mix and melt the material evenly.
- Injection: Once the plastic is molten, it is injected into the mold under high pressure, ensuring that it fills all cavities and achieves detailing.
- Cooling: The mold is cooled to allow the liquid plastic to solidify. This step is critical as the cooling time affects cycle time and overall production efficiency.
- Ejection: After cooling, the mold opens, and the finished part is ejected. This step may involve additional mechanisms such as ejector pins or plates.
The Advantages of Plastic Injection Molding
The plastic injection molding manufacturing process offers numerous benefits that make it advantageous for businesses in various sectors:
- High Efficiency: The ability to produce large quantities of parts in short cycles significantly boosts productivity.
- Cost-Effectiveness: Despite high initial setup costs for molds, the cost per unit decreases significantly with mass production.
- Complex Geometries: This process allows for intricate designs that might be difficult or impossible to achieve through other manufacturing methods.
- Material Versatility: A wide array of plastics can be injected, allowing for tailored material properties to meet specific requirements.
- Low Waste: Since the process involves precise material usage, it results in minimal waste compared to traditional methods.
- Environmentally Friendly: Advanced practices in plastic recycling and reusing scrap help mitigate environmental impacts.
Applications of Plastic Injection Molding
Plastic injection molding is utilized across various industries. Here are some notable applications:
1. Consumer Products
Nearly every household contains products manufactured via injection molding, including kitchen items, toys, and household appliances.
2. Automotive Industry
Automakers rely on injection molding for producing a plethora of components, from dashboards and mirrors to battery casings and connectors, enhancing both performance and aesthetics.
3. Medical Devices
In the medical field, precision molded plastics are crucial for producing devices such as syringes, packaging, and instrument housings, ensuring safety and compliance with regulations.
4. Industrial Applications
Injection molding is also vital in industries for fabricating components like gears, housings, and other mechanical parts, ensuring strength and reliability.
Future Trends in Plastic Injection Molding
As technology progresses, the landscape of plastic injection molding manufacturing continues to evolve. Here are some key trends to watch:
- Automation: The trend towards automation and smart manufacturing is expected to enhance efficiency and reduce production costs.
- 3D Printing Integration: The integration of 3D printing technologies is enabling rapid prototyping and more complex mold designs.
- Sustainability: Increasing emphasis on eco-friendly materials and processes is expected to reduce the environmental impact of plastic manufacture.
- Advanced Materials: The development of new materials, including bioplastics and advanced composites, will enhance the functionality of injection molded products.
Choosing the Right Injection Molding Partner
When considering plastic injection molding manufacturing, selecting the right manufacturing partner is crucial. Here are key factors to evaluate:
1. Expertise and Experience
Assess the company’s experience in the industry. A partner with a proven track record can offer valuable insights and reliability.
2. Technology and Machinery
Evaluate the technology and machinery they use. Advanced equipment allows for improved precision and efficiency.
3. Quality Control Processes
Ensure that the partner has robust quality control processes in place to maintain high-quality standards across all orders.
4. Customer Support
Strong customer service and support can make a significant difference in smooth project execution and resolution of any issues that arise.
Conclusion
The field of plastic injection molding manufacturing represents a cornerstone of modern manufacturing processes, offering businesses unparalleled advantages in efficiency, cost-effectiveness, and versatility. Industries from consumer goods to high-tech medical devices benefit from this technology’s precision and scalability.
For businesses looking to integrate plastic injection molding into their production processes or seek a trustworthy partner, DeepMould.net provides expert solutions tailored to your needs. Embracing this innovative manufacturing method can not only enhance your product offerings but also position your business competitively in the market.