Comprehensive Guide to Emergency Escape Breathing Apparatus Inspection
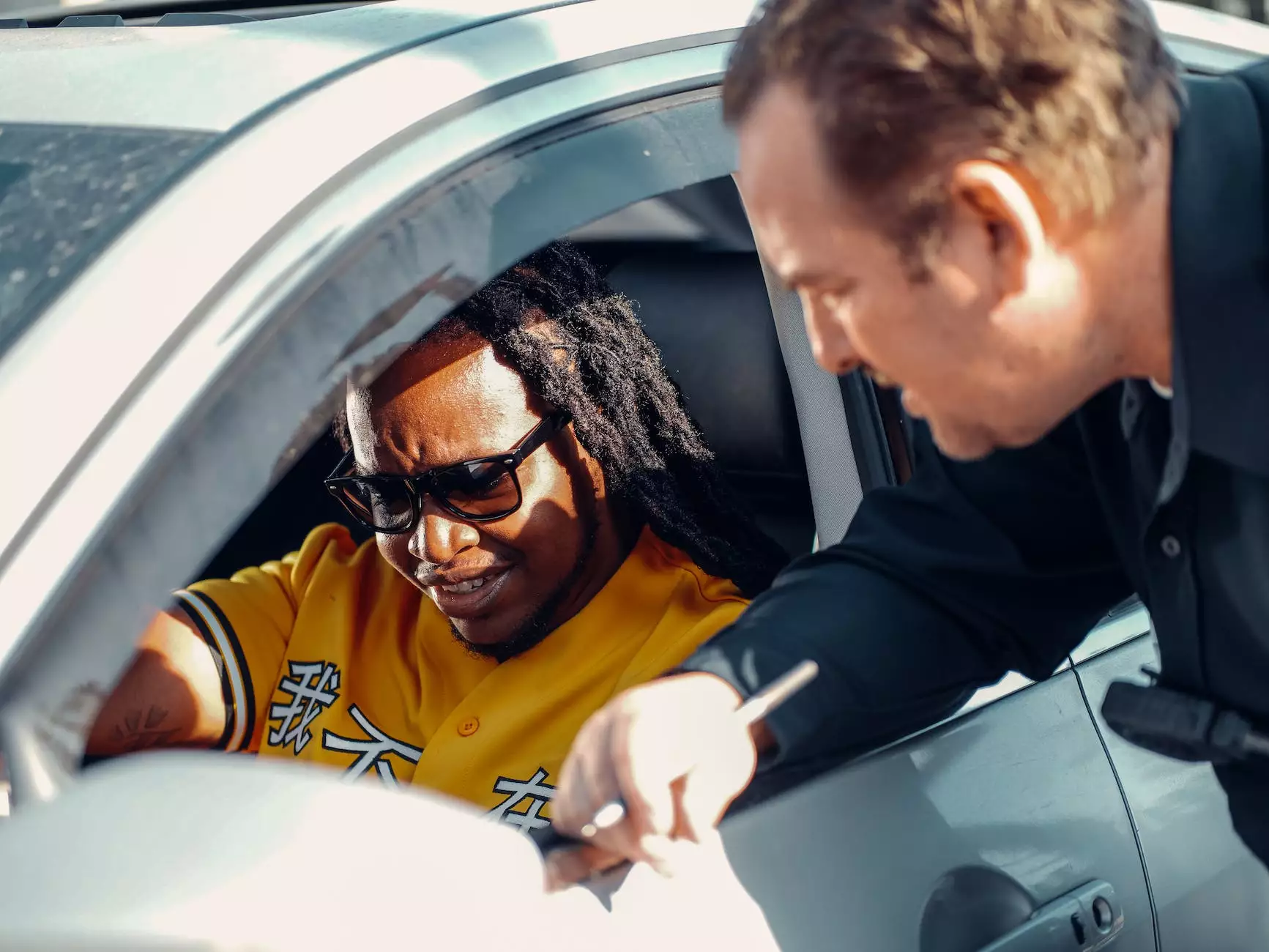
Introduction to Emergency Escape Breathing Apparatus
The concept of Emergency Escape Breathing Apparatus (EEBA) is critical in ensuring safety in environments where hazardous gases, smoke, or a lack of breathable air may pose a risk to health. First responders, industrial workers, and other professionals rely on this vital apparatus to escape dangerous situations. With the increasing awareness of workplace safety, the need for emergency escape breathing apparatus inspection has gained significant importance.
Understanding the Need for Inspections
Regular inspections of EEBA are not merely a suggestion but a requirement dictated by safety regulations and best practices. These inspections ultimately protect lives and property. Here are key reasons why emergency escape breathing apparatus inspection is essential:
- Ensures Functionality: Regular inspections guarantee that the equipment is in proper working condition, ready for use when necessary.
- Compliance with Regulations: Following local, national, and international codes enhances organizational safety standards.
- Maintains Equipment Integrity: Inspecting for wear and tear prolongs the life of the apparatus and reduces costs in the long run.
- Boosts Confidence Among Users: Knowing that equipment is regularly checked provides peace of mind to its users.
The Inspection Process Explained
The process of emergency escape breathing apparatus inspection consists of several essential steps. Each stage requires attention to detail to ensure overall safety and reliability:
1. Visual Inspection
The first step is a visual examination of the apparatus. Inspectors should look for:
- Physical Damage: Cracks, dents, or other signs of physical trauma.
- Corrosion: Especially on metal parts that may affect overall functionality.
- Proper Labels: Ensure all instructional labels and markings are legible and intact.
2. Functional Testing
This stage involves testing the components of the EEBA to confirm they are operational:
- Valve Operation: Check if the valves are closing and opening correctly.
- Pressure Testing: Ensure that the apparatus maintains the designed pressure levels.
- Alarm Systems: For models equipped with alarms, these must be tested to confirm they sound when needed.
3. Component Checks
The various components of the EEBA must be closely studied:
- Batteries: If applicable, check battery charge and condition.
- Filters: Ensure the filters are clean and functional to provide breathable air.
- Harness Systems: Examine straps and belts for wear and ensure proper functionality and comfort.
4. Documentation and Reporting
Once the inspection is complete, documentation is crucial. Records should include:
- Date and Time: Document when the inspection occurred.
- Inspector's Details: Include the name and qualifications of the inspector.
- Findings and Recommendations: Summarize any observations and suggested actions for any issues found.
Regulatory Standards Governing Inspections
Organizations must comply with various national and local guidelines that dictate how emergency escape breathing apparatus inspections should be conducted.
- Occupational Safety and Health Administration (OSHA): Provides regulations on the necessary inspections to ensure the safety of workers.
- National Fire Protection Association (NFPA): Sets comprehensive guidelines for testing and maintaining firefighting equipment, including breathing apparatus.
- American National Standards Institute (ANSI): Provides standards that cover safety requirements for emergency escape equipment.
Benefits of Compliance
Adhering to these regulations not only protects lives but also helps organizations avoid legal repercussions, reducing the risk of penalties. Compliance leads to:
- Improved Safety Culture: Promotes a proactive approach to safety within the organization.
- Increased Efficiency: Well-maintained equipment functions better and is more reliable.
- Enhanced Reputation: Organizations known for safety attract better talent and clients.
Best Practices for Effective Inspections
To maximize the effectiveness of EEBA inspections, consider implementing the following best practices:
1. Schedule Regular Inspections
Create a calendar for regular checks, ensuring that no apparatus is overlooked. Incorporating systematic inspections lets organizations stay ahead of potential issues.
2. Train Inspectors Thoroughly
Organize regular training sessions for personnel involved in inspecting EEBA. They must be aware of the latest technologies and regulatory standards.
3. Utilize Checklists
Develop comprehensive inspection checklists to ensure every detail is covered, from physical inspections to functional tests. This promotes consistency and thoroughness.
4. Engage Qualified Professionals
If resources allow, hire third-party professionals who specialize in emergency escape breathing apparatus inspection to conduct audits. This independent perspective can ensure compliance and safe practices.
Conclusion: The Imperative of Safety
In conclusion, the importance of emergency escape breathing apparatus inspection cannot be overstated. It is not just about meeting regulatory standards but fundamentally about saving lives and ensuring that in times of crisis, every individual has a reliable means to escape danger. By committing to regular inspections, adhering to guidelines, and implementing best practices, organizations can significantly improve their emergency preparedness and response capabilities.
The professional demand for effective educational services in areas of safety, including emergency escape breathing apparatus inspection, continues to grow. Organizations should prioritize training their workforce, as doing so enhances overall capabilities and confidence in emergency situations.
© 2023 H2S Online Training. All rights reserved.