Precision CNC Machining Factories: Revolutionizing Metal Fabrication
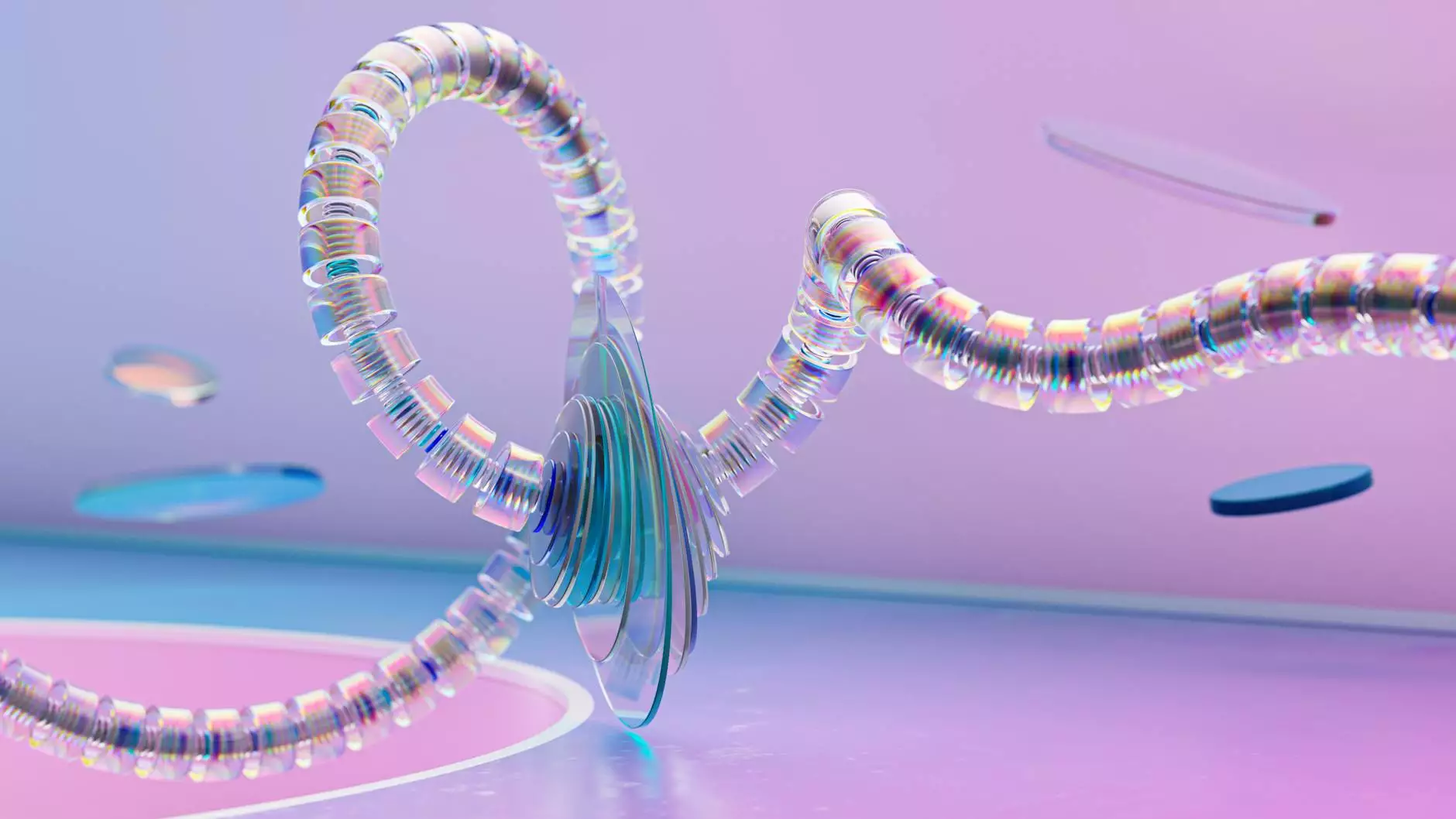
Precision CNC machining factories have transformed the landscape of modern manufacturing. In today's competitive market, businesses must leverage the most advanced machining technologies to meet customer demands for quality, efficiency, and cost-effectiveness. This article delves into the core concepts surrounding precision CNC machining, its benefits, and strategic insights for choosing the right factory for your metal fabrication needs. Moreover, we will explore how Deepmould.net fits into this picture as a leading enterprise in the realm of metal fabrication.
Understanding CNC Machining
CNC (Computer Numerical Control) machining is a manufacturing process that uses computer-controlled machines to precisely cut, shape, and finish materials, often metals, into desired specifications. The process can significantly enhance accuracy and repeatability, making it a vital technology for industries ranging from aerospace to automotive.
How CNC Machining Works
The CNC machining process involves several steps:
- Design: It begins with the creation of a CAD (Computer-Aided Design) model that outlines the product specifications.
- Programming: Engineers convert the CAD model into a CNC program, which includes the instructions for the machining tool.
- Setup: The machine is set up with the necessary tools, and the material to be machined is secured.
- Machining: The CNC machine executes the program, carefully cutting and shaping the material according to meticulous specifications.
- Finishing: Post-machining processes may include polishing, coating, or additional operations to meet the final product standards.
Key Benefits of Precision CNC Machining Factories
The rise of precision CNC machining factories can be attributed to several compelling advantages:
- Enhanced Precision: CNC machines offer high levels of accuracy, often within thousandths of an inch, which is essential for intricate components.
- Increased Efficiency: Automated processes reduce the time required for production, allowing for higher output without sacrificing quality.
- Consistency: CNC machining ensures uniformity in production, minimizing variations and defects.
- Flexibility: These systems can be easily reprogrammed for different designs, allowing factories to adapt to changing market conditions.
- Complex Geometry: CNC machines can create complex shapes and features that would be impossible or too costly with traditional machining methods.
Different Types of CNC Machines
Precision CNC machining factories utilize a variety of machines tailored for specific applications:
1. CNC Milling Machines
CNC milling machines are versatile tools used for a wide array of materials. They can produce intricate details and complex shapes by moving the material against cutting tools.
2. CNC Lathes
CNC lathes are primarily used for creating cylindrical parts. They rotate the material against cutting tools while it is shaped into desired dimensions.
3. CNC Plasma Cutters
This machinery is ideal for cutting conductive materials. CNC plasma cutters are effective for cutting thick metal sheets with precision.
4. CNC Laser Cutters
CNC laser cutting machines use a laser beam to cut materials with extreme accuracy. They produce clean edges and are ideal for detailed work.
Choosing the Right CNC Machining Factory
Selecting the proper machining factory is crucial for achieving the desired balance of quality, cost, and delivery time. Here are factors to consider:
1. Expertise and Experience
Look for factories with a proven track record in your industry. Their experience can influence the quality and reliability of the final product.
2. Technology and Equipment
Examine the types of machines and technologies employed by the factory. State-of-the-art equipment ensures precision and efficiency.
3. Quality Assurance Systems
A solid quality assurance system is essential. Factories should adhere to industry standards and certifications to guarantee product quality.
4. Communication and Support
Effective communication is vital for a seamless manufacturing process. Choose a factory that works closely with clients to accommodate their specific needs.
5. Cost and Value
While cost is a significant consideration, it should not overshadow the value offered by the machining factory. Assess the balance between quality and price.
The Future of Precision CNC Machining
The landscape of precision CNC machining factories is evolving rapidly due to advancements in technology. Major trends include:
1. Integration of AI and Machine Learning
The incorporation of artificial intelligence is revolutionizing CNC machining. These technologies enhance production efficiency by predicting maintenance needs and optimizing machining processes.
2. Additive Manufacturing
As additive manufacturing (3D printing) continues to grow, CNC factories are increasingly looking to integrate these two technologies. This fusion allows for more complex designs and reduced waste.
3. Smart Manufacturing
The Internet of Things (IoT) enables machines to communicate, thus enhancing factory automation and data collection. This leap towards smart manufacturing is making CNC machining more efficient than ever.
Conclusion
Precision CNC machining factories represent a critical component of the modern manufacturing sector. Their ability to produce high-quality, complex components with efficiency and consistency places them at the forefront of industry innovation. As the sector continues to evolve, companies like Deepmould.net are poised to leverage these advancements, providing exceptional solutions for all metal fabrication needs.
By understanding the intricacies of CNC machining—from its operational processes to its emerging trends—businesses can make informed decisions when enhancing their production capabilities. Partnering with the right precision CNC machining factory is essential for ensuring quality and satisfactory outcomes in today’s demanding market.