CNC Turning Metal Part Factory: Excellence in Metal Fabrication
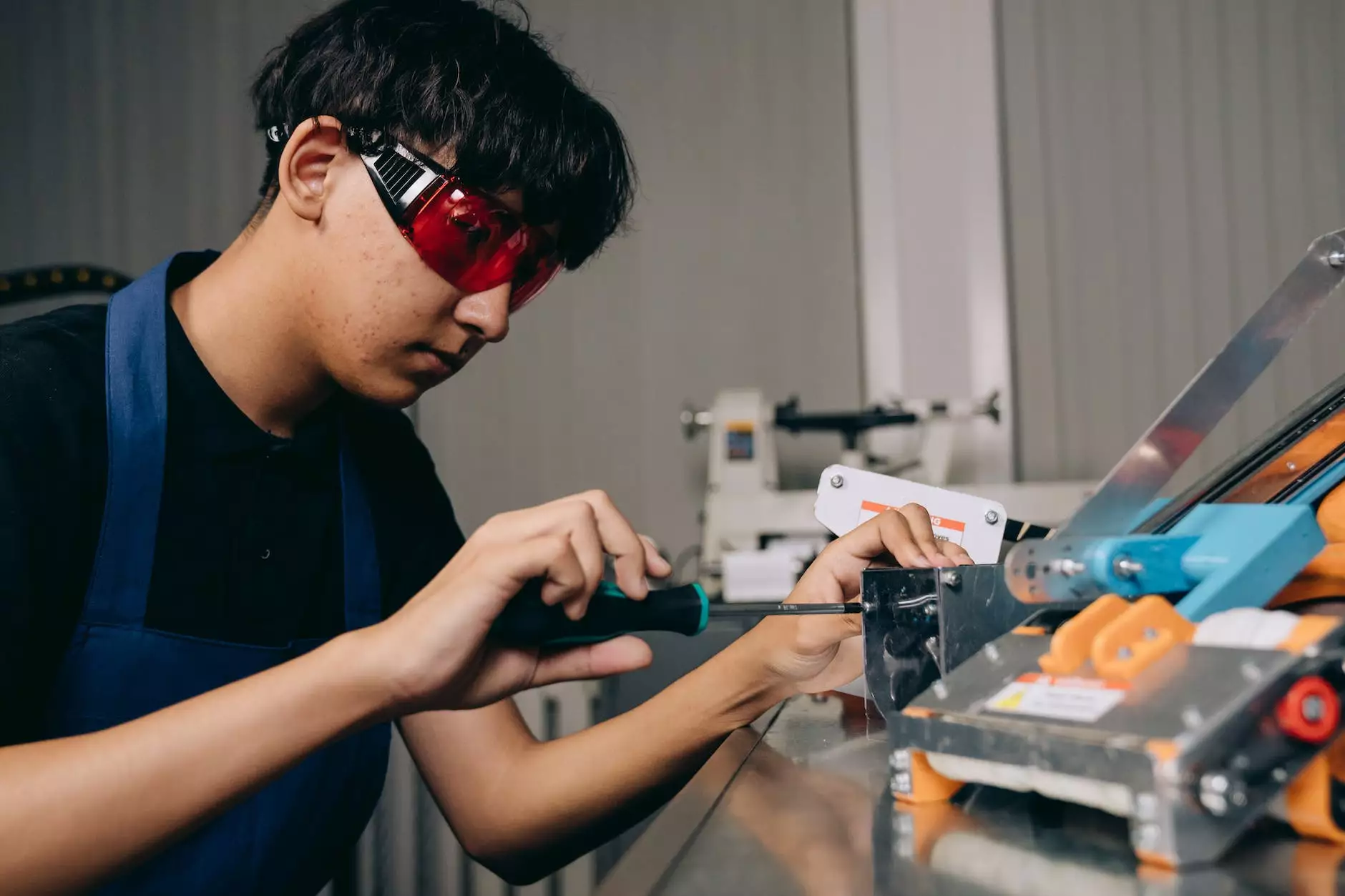
The demand for precision-engineered components is on the rise, driven by advanced technologies and evolving market needs. In this context, a CNC turning metal part factory stands at the forefront of manufacturing innovation, delivering intricately machined parts that meet the highest standards. Understanding the processes, benefits, and capabilities of these facilities is vital for businesses looking to leverage quality metal fabrication solutions.
Understanding CNC Turning
CNC (Computer Numerical Control) turning is a precision machining process that transforms raw metal into custom parts through a series of automated movements. Utilizing high-tech machinery, a CNC turning metal part factory can produce components with exceptional accuracy and consistency. The process involves several key stages:
1. Material Selection
The first step in any machining project is selecting the right material. Common materials used in CNC turning include:
- Aluminum: Lightweight with excellent machinability.
- Steel: Known for its strength and versatility.
- Brass: Offers good corrosion resistance and machinability.
- Plastic: Used for industry-specific applications where weight reduction is essential.
2. Designing the CAD Model
Every CNC project begins with a Computer-Aided Design (CAD) model. This digital representation of the part outlines dimensions, tolerances, and geometries that need to be replicated during machining. The CAD model plays a crucial role in visualizing the end product and ensuring precise specifications are met.
3. Programming the CNC Machine
Once the CAD model is finalized, it is converted into a Computer Numerical Control (CNC) program. This program includes coded instructions that guide the cutting tools through the necessary paths to create the desired part shapes. Effective programming is fundamental in ensuring smooth operations within the manufacturing process.
4. Machining Process
During the actual machining process, the CNC machine spins the workpiece while various cutting tools are applied to achieve the necessary dimensions and surface finishes. This operation is often referred to as CNC turning, as it involves the continual rotation of the metal part. The process can incorporate several techniques, including:
- Facing: Smoothing the end face of the part.
- External Turning: Shaping the outer diameter of the material.
- Internal Turning: Boring out the internal dimensions of the part.
- Threading: Creating threads on the material.
5. Quality Control
Quality assurance is paramount in a CNC turning metal part factory. After machining, each part undergoes rigorous inspection using precision measuring tools to ensure they meet the specified tolerances and quality standards. This step prevents defects and ensures customers receive only the best products.
The Advantages of CNC Machining in Metal Fabrication
Utilizing a CNC turning metal part factory offers numerous advantages over traditional machining methods. These benefits significantly enhance the overall manufacturing process for businesses across various sectors.
Precision and Accuracy
CNC machines are known for their remarkable precision. They can produce parts with tolerances as tight as ±0.001 inches. This level of accuracy is vital in sectors such as aerospace, automotive, and medical, where even minute discrepancies can lead to catastrophic failures.
Consistency and Reproducibility
Once programmed, CNC machines can replicate identical parts indefinitely without any variation in quality. This aspect of machining is crucial for businesses that require large volumes of components, ensuring that each piece meets the same standards of excellence.
Complex Design Capabilities
The advanced capabilities of CNC turning allow manufacturers to create complex geometries and intricate designs that would be practically impossible to achieve using traditional methods. This flexibility enables innovation in product design, opening new opportunities for businesses in various industries.
Reduced Human Error
By automating the machining process, CNC turning metal part factories minimize human error. While manual machining relies on the skill and experience of the operator, CNC technology allows for consistent performance, significantly reducing the likelihood of mistakes.
Applications of CNC Turning in Different Industries
The versatility of CNC turning makes it a preferred choice across multiple industries. Here are some key sectors that benefit from this technology:
Aerospace
The aerospace industry demands high precision and reliability. CNC turning is utilized to manufacture critical components such as engine parts, housings, and brackets with impeccable accuracy to withstand extreme conditions.
Automotive
In the automotive sector, CNC turning produces various parts such as axles, shafts, and valve bodies. The ability to create lightweight yet strong components aids in enhancing fuel efficiency while maintaining performance standards.
Medical Devices
Medical industries rely on CNC turning to produce surgical instruments and implants. The strict quality and cleanliness standards upheld by manufacturers ensure that these parts are safe for patient use.
Industrial Machinery
CNC turning is integral in fabricating components used in industrial machinery, such as gears, pulleys, and brackets. These parts must exhibit robust performance and high durability to meet demanding operational requirements.
Choosing the Right CNC Turning Metal Part Factory
When selecting a CNC turning metal part factory, consider these factors to ensure you partner with a capable manufacturer:
- Industry Experience: Choose a factory with a proven track record in your specific industry.
- Technology and Equipment: Ensure they utilize state-of-the-art CNC machinery for the best results.
- Quality Assurance: Look for certifications and a comprehensive quality control process to guarantee the excellence of the components.
- Custom Capabilities: Verify that they can handle your unique design requirements and production volumes.
- Customer Support: Strong communication and support are vital for a successful partnership.
The Future of CNC Machining
The future of CNC turning metal part factories looks promising, with emerging technologies reshaping the landscape of manufacturing. Industry 4.0, characterized by smart manufacturing, is integrating artificial intelligence, IoT, and advanced robotics into machining processes. This innovation drives efficiency, reduces lead times, and enhances customization capabilities.
Advancements in Technology
As technology evolves, CNC machining techniques will continue to improve. Developments such as additive manufacturing, hybrid machining, and enhanced software for design optimization are expected to expand the capabilities of CNC turning, enabling the production of even more complex and intricate designs.
Sustainable Manufacturing Practices
With a growing emphasis on sustainability, CNC turning metal part factories will need to adopt eco-friendly practices. This includes the use of recyclable materials, energy-efficient processes, and waste reduction strategies. Embracing these practices not only benefits the environment but also enhances brand reputation among environmentally-conscious consumers.
Conclusion
In conclusion, a CNC turning metal part factory plays a crucial role in modern manufacturing, delivering precision, efficiency, and reliability. Businesses across various sectors can benefit from the exceptional capabilities of CNC machining, producing high-quality components that meet demanding specifications. With advancements in technology and a focus on sustainable practices, the future of CNC turning looks bright, paving the way for innovative solutions in metal fabrication.
For businesses seeking premium metal fabrication services, partnering with a leading CNC turning metal part factory like Deep Mould can facilitate excellence in their products. Explore our insights and leverage our expertise to enhance your manufacturing capabilities.